Success Story
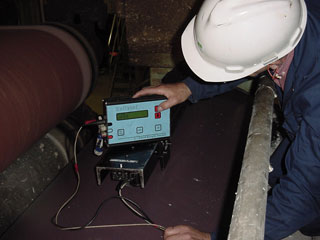
Rollprof: A powerful instrument for condition monitoring by measuring rolls inside the paper machine
Norske Skog Saugbrugs has used the Rollprof measuring system for several years to measure the wear and condition of their rolls inside their three paper machines. New roll measuring applications are discovered daily with the use of Rollprof inside the paper machine. It is your own imagination that sets the limits for the use of the Rollprof inside the machine.
Measuring of rolls inside the paper machine
Because of the additives in the pulp, paper machine rolls become worn over time. With the help of the Rollprof system it’s possible to measure the wear condition of the rolls inside the paper machine. Before using the Rollprof roll changes were scheduled on time or tonnage basis. It was difficult to establish the coating condition until the roll was removed and put in the grinder. This is a time consuming an expensive way of working.
Today, Norske Skog Saugbrugs changes most rolls based on their condition. Rolls with ceramic coating are changed based on the condition of edge wear. Rubber coated suction press roll which can swell or wear in the edges are measured in the same way. Current follow-up of new coatings will give an advantage by using this kind of system. The supplier of new coatings will have a quick response about the function of the roll.
The data from the measurement is easily downloaded into a PC. The data (length and height) will be displayed both graphically and numerical. Archived measurements are displayed on a “waterfall” graph to see the developing wear. The maintenance supervisor can get a print out directly from the Rollprof to be evaluated on the spot.
Measuring steel rolls in the calender section gives valuable information. The shift to changing steel rolls on condition has resulted in that the simplest rolls are in use for several years instead of only months.
The principles are the same for measurements made inside the paper machine. Active management and tracking of roll wear is achieved.
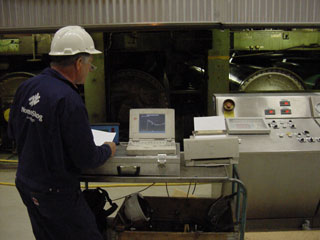
Measuring of the lower blade in the headbox is made with Rollprof. Incorrect profiles on the paper web is often caused by wear in the headbox. By using the Rollprof Beam system it’s easy to measure and control wear on the lower blade. This measuring has been a great help to schedule planned headbox maintenance and to aid in diagnosing blade malfunction.
Measuring wear on ceramic rolls is another area where the Rollprof is used extensively. Ceramic-coated rolls are often very expensive and there for it’s important to change them only when they need to be. It’s important to become aware of worn ceramic coatings that cause improper profiles on the paper web.
Circular measuring of rolls inside the machine is another area where the Profiler is used. Often it’s hard to decide how vibrations appear, and when they appear it’s important to quickly find the cause of the vibration. With Rollprof it’s easy to decide which roll that are oval. When a roll has been sent out for coating or repairs the Rollprof is used to measure the profile and check the supplier’s work before the roll is put back into production.
The Rollprof is used to establish if a roll has a bent shaft or a bent roll body. It’s important to know how the damage occurred and the severity of the problem. It’s possible to tell the supplier in advance of the damage by using Rollprof. This advance information will help in determining the repair costs. When using the same method Norske Skog Saugbrugs can ensure the quality of any repairs or rework.
Rollprof is also used as a measuring and checking instrument in the roll grinding and turning machines.
In this paper we’ve discussed some of the places where the Rollprof is used. The changes in the paper industry demand the need for fast and accurate measurement of rolls and other components in the paper machine. Making sure the product has the correct profile is critical in this highly competitive industry.
Our reference:
Jon-E. Melin
Norske Skog Saugbrugs
N-1756 Halden Norway
Tel.: +47 69 17 40 00
Fax: +47 69 17 43 30
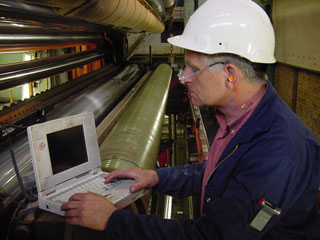